Sprayer manufacturers have all but offloaded the entire responsibility for drift management to the sprayer nozzle. It’s asking too much.
Sprayers have changed a lot over the past 25 years. They have become larger, with more tank capacity, boom width, and, if self-propelled, horsepower. They are more comfortable and ergonomic, with more sophisticated swath control and guidance systems. But every year, a very important deficiency in their design becomes obvious. Drift control.
The changes described above are intended to improve productivity and fight operator fatigue. Today’s sprayer can cover more ground than ever before. But the demand to cover ground, through a combination of growth in farm size and frequency of treatment, has outpaced machine productivity. As a result, operators find themselves ever further in a time deficit, with acres on the to do list and no time to get the work done.
Spray drift remains the single most limiting factor to the safe application of pesticides. Spraying cannot happen when it’s too windy or during inversions because all agricultural nozzles produce fine droplets whose movement in the atmosphere cannot be controlled . This has been an issue since spraying began.
Simply put, pesticides belong in one place only, and that is on the treated swath. Applicators have some tools to make this happen, such as using coarser sprays, lowering the booms, choosing very specific weather conditions, and the like. But when winds are incessant, and crops and pests are quickly growing out of the treatable stages, what is an applicator to do? There is only one thing they can do: lower their standards. Either miss the treatment and suffer the yield loss, or spray in the wind and hope nothing bad happens.
Neither of these options are acceptable.
There isn’t an easy fix. Spraying is a game of tight margins. The spray liquid in the tank must be atomized in droplets that can make their way to the target and provide adequate coverage when they get there. The total liquid volume to achieve that task must also be practical. The global ag industry has determined, over the past 100 years, that about 100 to 200 L/ha, 10 to 20 gallons per acre, is the ballpark amount that allows reasonable work rates with sprays that are just coarse enough to resist displacement in modest winds. If it gets windier and we need even coarser sprays, we need to add more water to maintain an acceptable droplet density on the targets. And of course, the droplets need to stick to those targets, so there is a limit how coarse we can spray.
Over the past 20 years, we’ve been asking the low-drift nozzle to do the heavy lifting in drift management, and it has served us well. But with a return to more contact modes of action for resistance management, there’s a need to retain good coverage for product performance.
What ag needs is a drift-reducing technology that is better than the low-drift nozzle. We need a technology that maintains a practical water volume limit and combines this with intermediate spray qualities that generate good pesticide efficacy without allowing drift under windy conditions.
These technologies need to do just one of three things: (a) Protect the driftable droplets from exposure to moving air with a physical barrier, (b) make driftable droplets less drift-prone by increasing their velocity, or (c) eliminate the driftable droplets altogether.
Let’s have a look at some options, and explore the pros and cons.
- Shields and Cones. A shroud surrounding the boom was first proposed and built in the 1950s in the UK by Dr. Walter Ripper. Although never commercial, his “Nodrif” boom inspired an entire industry that took hold in western Canada in the 1980s and 1990s. Shrouding worked. In studies conducted at Ag Canada, shrouds produced by Flexi-Coil, Rogers Engineering, AgShield, and Brandt reduced drift by up to 80%. But shrouds disappeared in the 90s, partly because of the advent of tight-folding suspended booms where they posed a problem, but also because of crop contamination from the shrouds and poor nozzle visibility in case of plugs.
The advent of the air-induced low-drift nozzle offered an alternative, but coarseness has been taken to its practical limit. What about a newly engineered version of shrouds that addresses its shortcomings? Willmar Fabrication has created the Redball Buffer Sprayer, for example. We see hooded sprayers in row crops. But there may be other ideas. The simple device called the PatternMaster introduced by KB Industries a few years back was also a step in that direction. Let’s keep working on this.
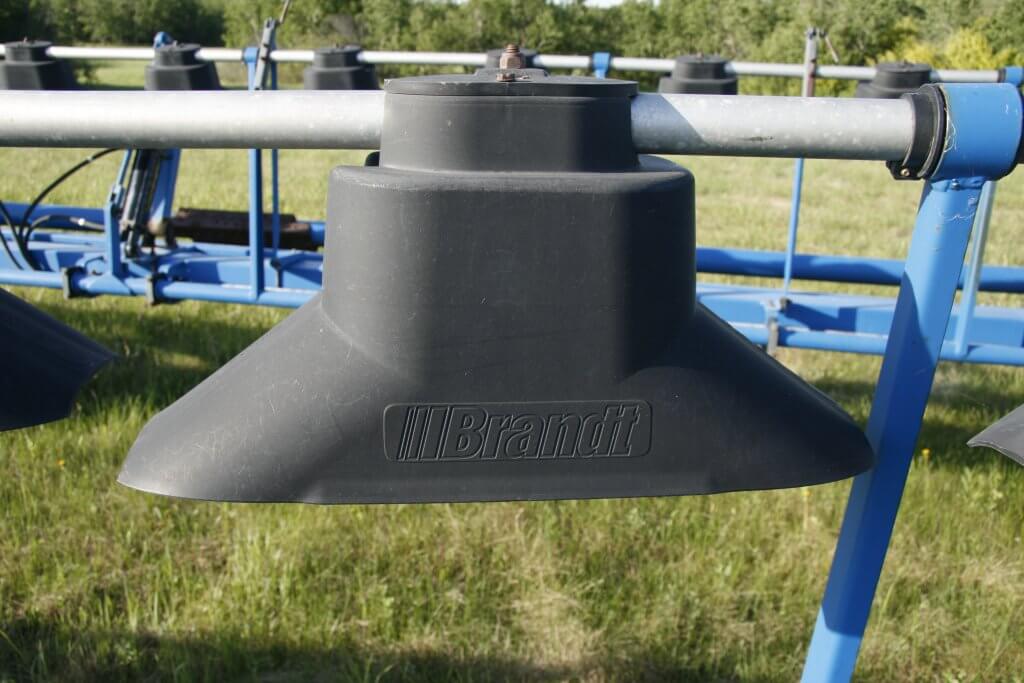
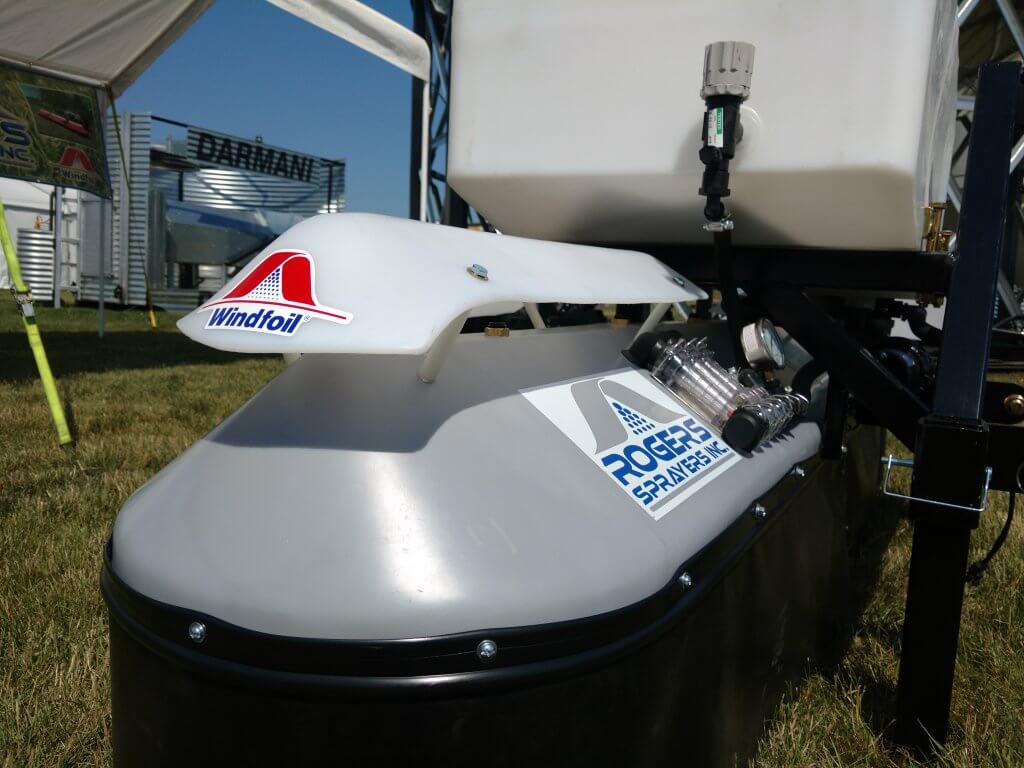
- Air Assist. Small drops don’t drift just because they’re small. They drift because they have very little kinetic energy, and they get blown off course easily. Speed them up, and that problem is solved. Introducing an air stream at the nozzle can do just that. Furthermore, air assist also enhances canopy penetration, a problem that we currently attempt to address with the addition of more water. Again, this idea is not new. Hardi, once the world’s largest sprayer manufacturer, has had the TwinForce boom available for decades. An inflatable bag is positioned over the boom. Openings along the bottom direct the air down. The operator turns a knob in the cab to control fan speed, and another for forward or backward angle, until the combination is suited to the canopy and the travel speed. The SprayAir, out of Carseland, AB (purchased by Miller and still available) was a less elegant version because they chose an air-shear atomizer that sometimes required more air than was prudent. Too much air rebounds off the ground, increasing the drift issue. Their Trident boom, allowing a hydraulic nozzle to be used with air assist, continues to have potential. Air bag type air assist systems were also available from other manufacturers, but none were ever commercially successful.
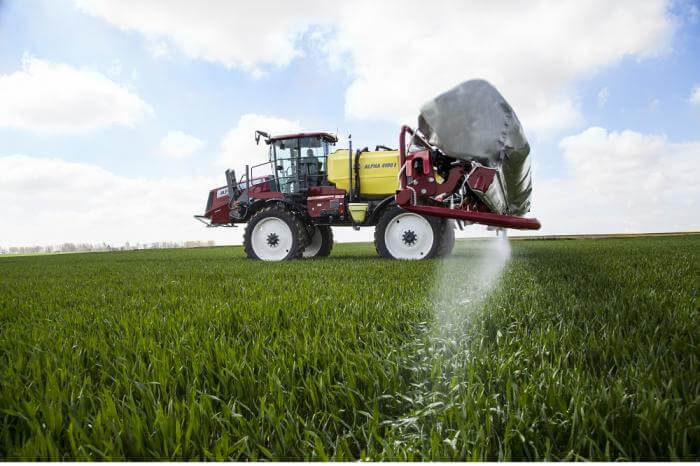
- Low Booms. How low can booms go? It depends on the nozzle spacing and fan angle. Horsch claims that with a good boom package, this is an option. They are offering 10” spacing, and with wide fan angles, booms as low as 15” would still provide good overlap. Hands up who will try this at 18 mph. Wingssprayer has an interesting design where the boom rests on backswept plastic sheets, providing a physical barrier and a low height.
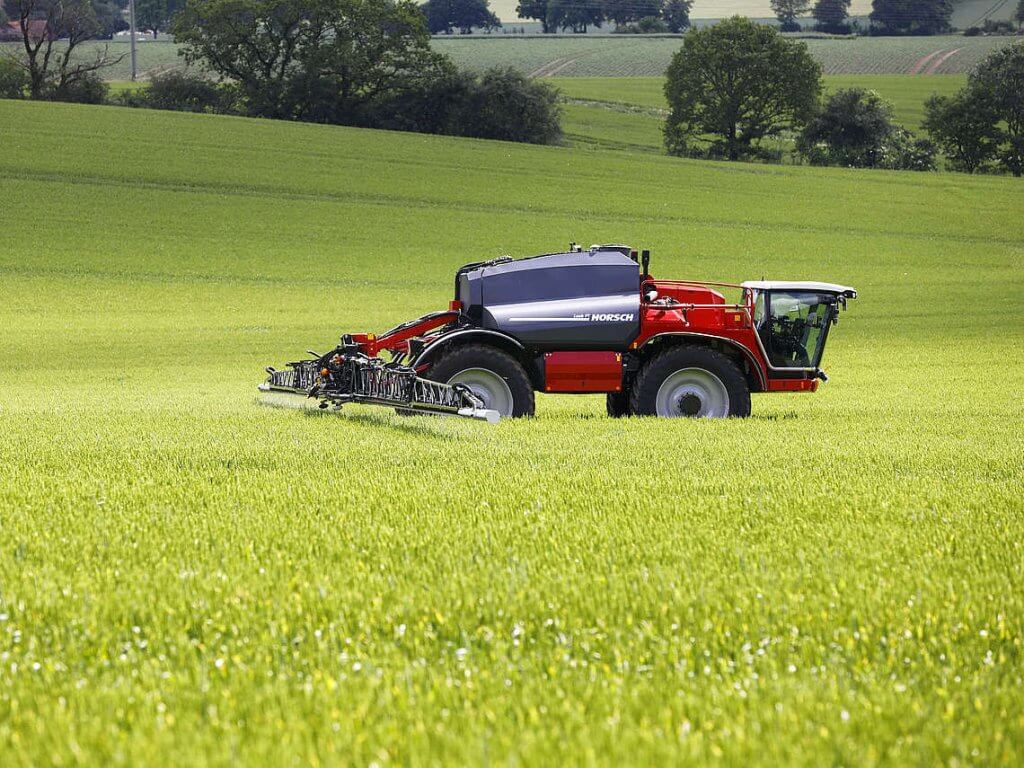
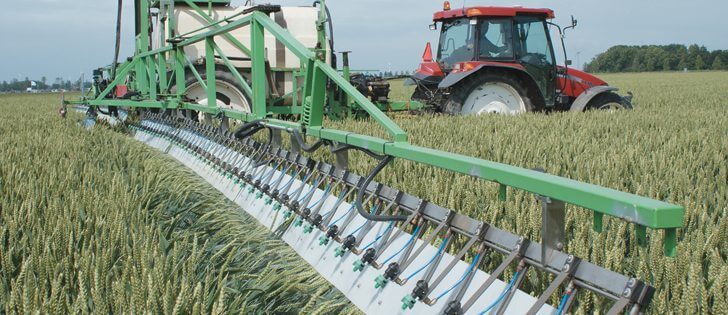
- Twin Fluid Atomizer. In this atomizer type, both air and liquid are forced out through the same nozzle. The ratio of air and liquid determines the liquid flow rate and the degree of atomization. First introduced by Cleanacres in the UK as the Airtec, improved by Harry Combellack in Australia over many years, and making a re-appearance with the Dutch manufacturer Agrifac, it’s been one of my favourite atomizers, mostly in theory. The small amount of air moving through each nozzle is not enough for serious air-assist, but the idea is good and perhaps it can be improved.
- Electrostatics. Forget about it for drift control. The attractive force is so weak that it only works for very small droplets over short distances. It needs air-assist to work properly. See point #2.
- Rotary Atomizer. These are all the rage on aircraft these days, offering a more consistent droplet size range that eliminates the largest, water-wasting droplets, and curtails many of the smallest droplets produced by hydraulic atomizers. These attributes are powerful and address the fundamental problem: If the small droplets drift, then let’s not produce them. In reality, rotary atomizers are used mainly to produce smaller droplets to save water in the aerial business, not really solving the drift problem. In the 1970s and 80s, the concept was advanced by Micron Corporation, led by Ed Bals and later by his son Tom. Although very successful in forestry and hand-held applications in arid regions where water posed a serious limitation, the transition to boom spraying never happened.
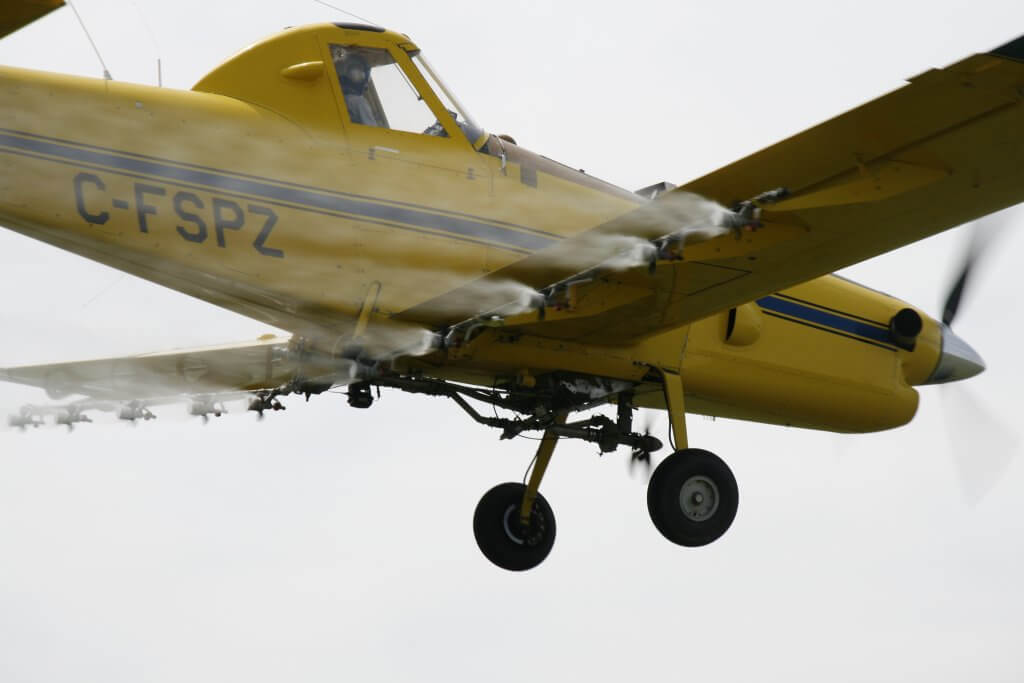
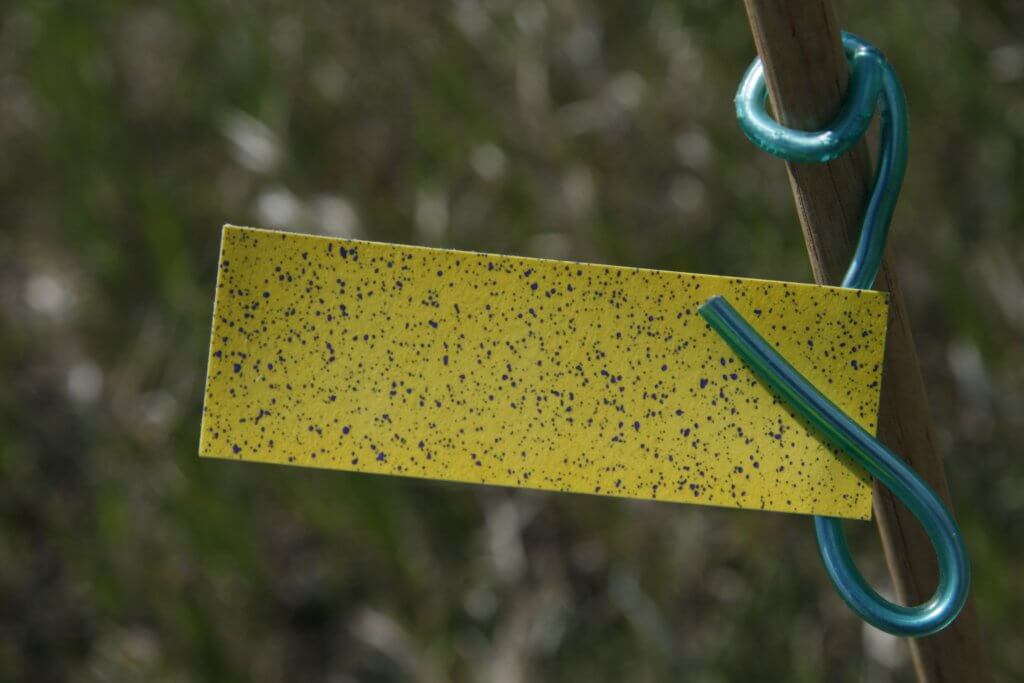
- A new Atomizer. This is my Hail Mary. All hydraulic nozzles produce a wide variety of droplet sizes, and that is a problem. Even the venerable dicamba nozzles that create Extremely Coarse and Ultra Coarse sprays produce some fines that drift in inversions. The idea put forth by Ed Bals, to eliminate the problematic size ranges, is sound. But the rotary atomizer is hard to implement on a boom sprayer. Can there be an innovation that maintains a simple overall design, produces a narrow, but low-drift droplet size range, and mates it to a bit of air assist to get the spray where it belongs? Absolutely.
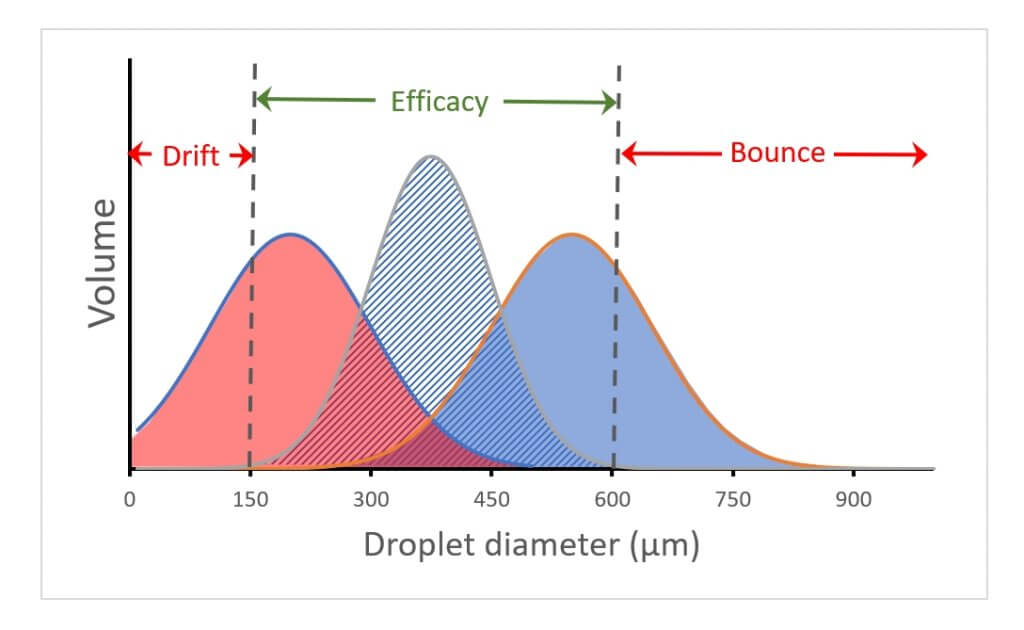
To create value for farmers you first need to understand farmers’ priorities and problems. Getting the spraying job completed on time often means squeezing the work into ever narrower time frame, between rains, between winds in the afternoons and inversions that same evening, between too much dew and too dry, between too early and too late. I am looking forward to the day when engineering resources are allocated to address these issues better, protecting both the environment and the stress levels on the farm.